Enhancing Operational Performance through Anomaly Detection and Predictive Maintenance
We developed a model for our customer to minimize machine downtime and increase production efficiency. Early anomaly detection results in predictive maintenance, which saves costs and reduces unplanned downtime.
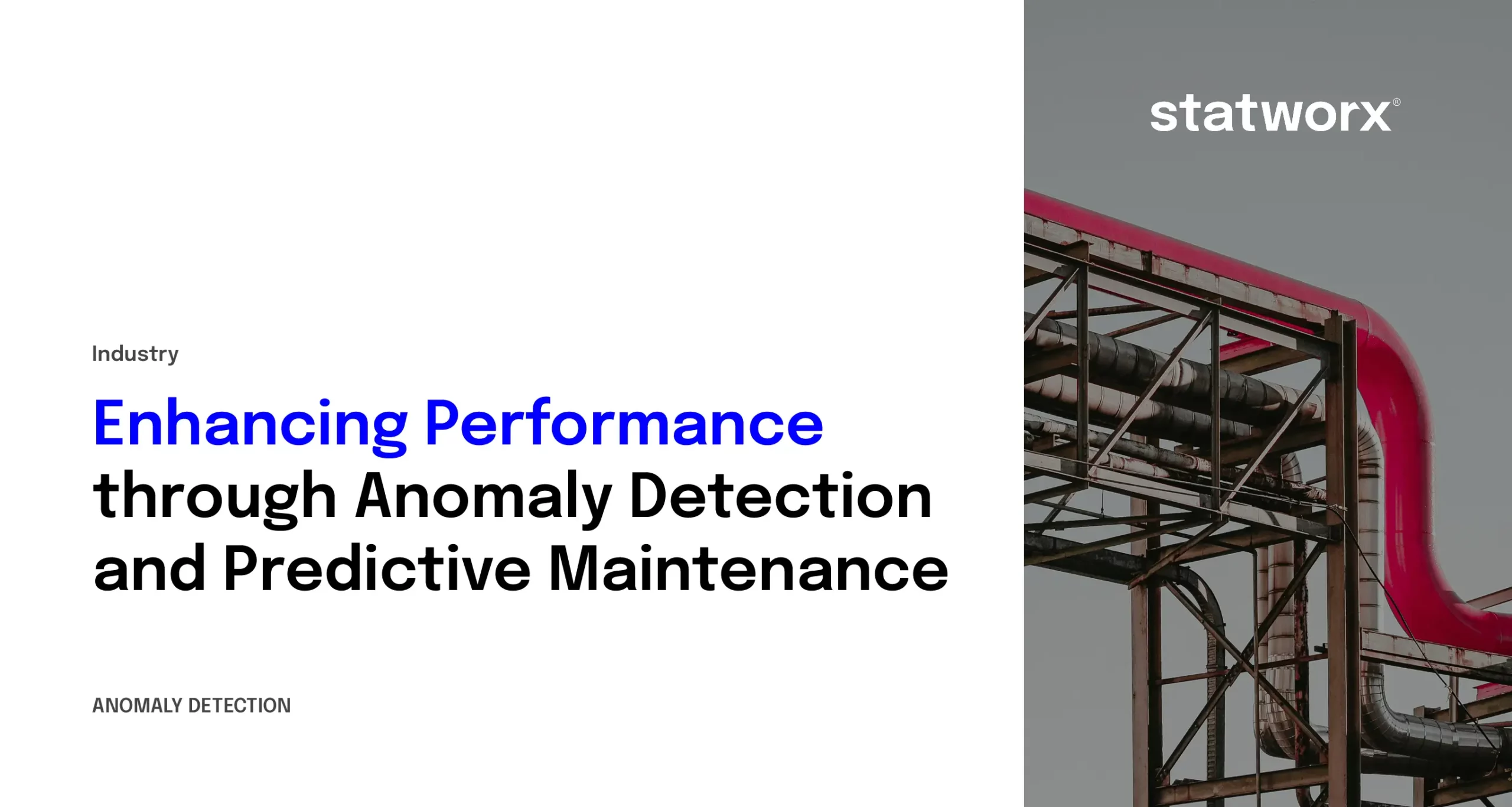
Challenge
Our customer was faced with the challenge of frequent unplanned machine failures, which led to significant production interruptions and high costs. The risks included production losses, increased maintenance costs, and potential reputation damage due to delivery delays. A solution was needed to ensure production continuity and optimize maintenance costs.
Approach
We developed a predictive model for early anomaly detection. To do this, we used advanced data analytics and machine learning to identify patterns and abnormalities in machine data. The solution was integrated into the customer's existing monitoring system and tested offline to identify artificially generated anomalies. In addition, the detected anomalies were automatically recorded, stored and classified.
Upshot
The developed model for anomaly detection showed almost real-time capabilities and was successfully validated in live tests. The implementation made it possible to carry out planned maintenance work more efficiently and significantly reduce unplanned downtime. The customer benefited from increased production efficiency and significant cost savings.